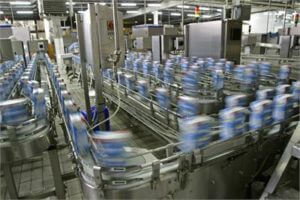
Five tips for designing electric actuators into food processing equipment
Machines used for food processing increasingly must be designed to meet ever-stringent requirements to keep food clean during production and ensure it arrives safely to the consumer. Hygienic actuators are a key ingredient to help maintain the highest standards for health and safety.
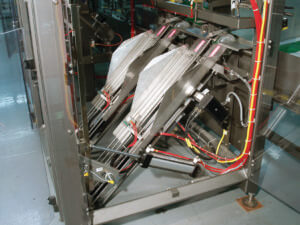
In the bag
Rodless electro-mechanical actuators on a modular bagging system precisely position incoming bags regardless of size.
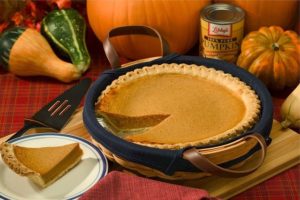
Easy as pie
Five best practices for designing and installing electric actuators in food processing equipment help create open/clean-in-place designs.
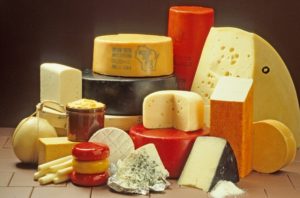
Cheese-making: Automating an ancient art for safety and efficiency
Electric linear motion enhances cheese processing and production.
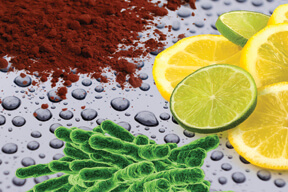
Linear motion for meat processing
Linear actuators used in meat processing are designed for corrosion resistance, washdown protection and bacterial growth prevention.
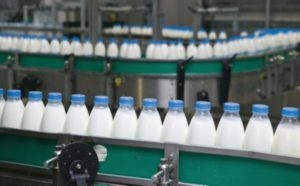
The case for electric rod actuators in food processing applications
Producing food that’s delicious, affordable and safe requires a lot from manufacturers. Process automation makes affordability possible and ensures consistently top-quality food. Safe food products and beverages are free of contamination, so the equipment used in food processing has to meet crucial requirements for cleanliness. That includes linear actuators.
Selecting a linear actuator for a food processing application requires careful consideration. A machine designer may look at hydraulic cylinders, pneumatic cylinders, rodless electromechanical actuators and electric rod actuators.
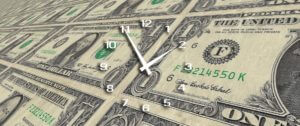
Electric cylinders speed up food processing operation
From food processing plants to machine shops, there’s a constant drive for greater efficiency, faster turnaround and less downtime. Everyone is involved in the effort, from design engineers who develop equipment to plant engineers who manage processes. In food processing operations, the need for speed translates into things like faster operation, easier cleaning, greater accuracy and less maintenance. Electric linear actuators and electric cylinders used in these plants need to meet specific standards.
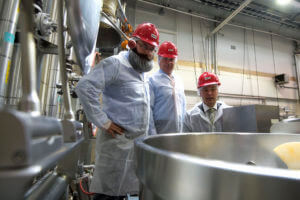
Keeping it clean: hygienic linear actuators for food safety
Cleanliness is serious business in food processing. The potential for contamination by microbes, chemicals and other foreign substances is real and always present. And food residue can be hard to eliminate. Keeping processing equipment clean makes good business sense. (Nobody wants their brand associated with foodborne illness.) Plus, the Food Safety Modernization Act (FSMA) makes it part of the law of the land. Food processors rely on their equipment to withstand the rigors of the processing environment. That’s especially true for hygienic linear actuators for food safety.
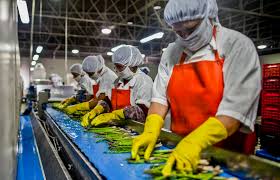
What to consider: electric actuators for food and beverage processing
Keeping things clean is a top concern in food and beverage processing operations because food safety is crucial. The Food Safety Modernization Act (FSMA), with its emphasis on preventing foodborne illness, puts even more pressure on food producers. Machine designers who serve this industry need to incorporate components that meet the industry’s demands. When it comes to electric linear actuators, there are several things a design engineer needs to consider, especially if the machine will be subjected to periodic washdowns.
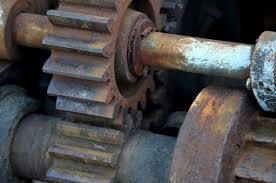
Stainless steel linear actuators stand up to corrosion, tough conditions
Machine designers who develop systems for harsh environments often need corrosion resistant components, including stainless steel linear actuators, to stand up to challenging environmental conditions. Corrosive agents, moisture and dust in manufacturing environments impact the performance and life of automationn components. Dust and debris may enter housings causing wear. Moisture may short electrical connections. Corrosive agents can eat away at housings, seals, fasteners and more. For confirmation that a component will stand up to environmental factors, we recommend the IP (International Protection or Ingress Protection) rating system.
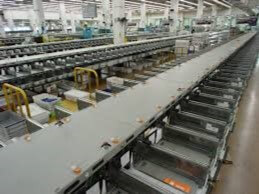
Electric cylinders essential to advanced conveyor system [Case Study]
Conveying systems are common in manufacturing. They can be straight-forward systems that take packages from point A to point B or complex ones for sorting and diverting. Systems used in food processing also must handle washdowns, a common practice in the industry.
As critical components, linear actuators must withstand the challenges of the application including environmental ones. Pneumatic cylinders have been used extensively in conveying. However, electric cylinder use is growing, fueled by demand for programmability and better accuracy.
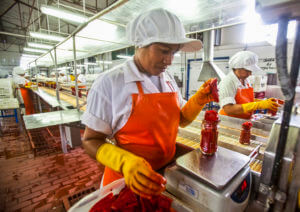
Machine design, FSMA, and electric rod actuators
Machine designers who serve the food processing industry face a huge opportunity. Purchases of equipment are expected to grow 7% a year to around $70 billion by 2020.
Not surprisingly, consumer demand is fueling this growth, but equally important in the U.S. is the Food Safety Modernization Act or FSMA. This legislation requires that food processors be proactive on food safety, that is, they must identify potential hazards and mitigate them.
A major result of the FSMA has been stepped up cleaning requirements and increased demand for hygienic equipment. That equipment needs washdown-ready components like electric rod actuators.
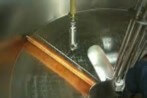
Machine design, clean in place (CIP) and linear actuators
Keeping clean is important, right? Well, in food and beverage processing and pharmaceuticals manufacturing keeping equipment clean is essential. Cross-contamination among batches causes problems, and food or beverage residue can grow harmful microorganisms. Many plants have clean in place (CIP) systems that deliver cleaning tailored to the needs of the facility including cleaning action (force, turbulence, direction), timing/duration (when, how often, how long), temperature, and type/strength of cleaning agent.
When you design equipment for these industries you need to keep cleanability in mind. Even components like electric linear actuators must stand up to cleaning procedures.
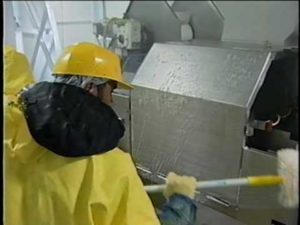
Electric linear actuators meet the challenge of FSMA
The federal Food Safety Modernization Act (FSMA) that was enacted in 2011 has energized the food industry around food safety and the prevention of food-borne illnesses. Most of the major producers and food equipment manufacturers have kept ahead of FSMA requirements successfully since food safety and prevention have always been among their top priorities.
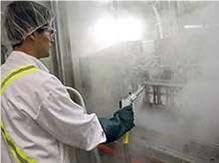
Electric linear actuator is clean-in-place, washdown ready
Stringent regulations govern the food processing industry. Food processing equipment and components, like electric linear actuators, must meet food safety regulations and stand up to clean-in-place (CIP) procedures. Food industry cleaning procedures may include regular washdowns with hot water, steam, high pressures, and caustic chemicals. Corrosion resistant materials and a water-shedding design are musts.
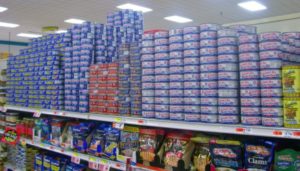
Hygienic linear actuator keeps it clean
The world of food production and packaging is broad, varied and ever-changing. That world needs filling machines as diverse as the range of food products they process. Some filling machines have to handle powders and dry solids while others must handle thin or thick liquids. Some machines fill to a specified level, and some fill by volume or weight. This wide variety of equipment has a unifying need, though -- a need for hygienic design that can keep food products uncontaminated and withstand even the most stringent cleaning procedures.
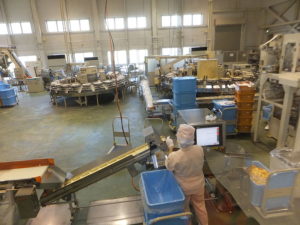
Linear actuators help prevent food contamination
Until recently, the food processing industry has handled contamination reactively. If a foodborne illness was traced back to contamination at a manufacturing plant, the FDA (Food and Drug Administration) had the manufacturer fix the problem.
The flaw in this system, though, was that most of these illnesses were preventable. The Centers for Disease Control and Prevention estimates that 48 million people (1 in 6 Americans) get sick, 128,000 are hospitalized, and 3,000 die each year from foodborne diseases. That makes food contamination a major public health issue.
The federal government stepped in to change the way the FDA and food producers operate with the Food Safety Modernization Act (FSMA) – signed into law in January 2011. This important legislation shifts the focus to preventing contamination problems instead of just responding to them. FSMA affects all automation components used in the industry, including linear actuators.
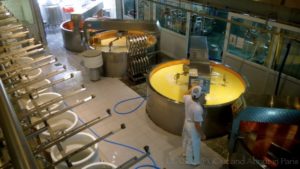
Hygienic, IP69K electric rod actuator meets food processing needs
Food processing is a tough environment for most automation equipment. There may be washdowns with high-pressure, high-temperature water. Caustic cleaning agents might be used. There also may be strict food safety standards to adhere to, like the USDA’s regulations for the meat, poultry and dairy industries. As automation components, all linear actuators, like electric rod actuators, need to stand up to the rigors of the food processing environment.
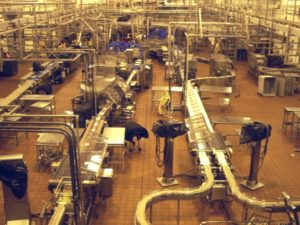
Linear actuator reduces energy use in food & beverage processing
Once upon a time, managers of food and beverage processing plants considered energy costs to be a basic cost of doing business – something out of their control. But several factors have changed that attitude. Among them are rising energy prices, a challenging economy and an emphasis on reducing the environmental impact of manufacturing facilities.
Processors now see energy use as a cost that can and should be strategically managed. Companies are trying to optimize their energy budgets – increasing their plants’ energy efficiency, reducing use and looking for lower cost, cleaner energy sources. They're also looking at the energy use of all machinery and automation components like linear actuators.
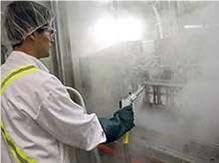
VIDEO: Selecting an electric linear actuator for safe food processing
The food processing industry is fanatical about safety. Producers want to be known for offering safe and delicious products. In addition, governments want to protect their populations against illnesses caused by contamination and food-borne microbes.
In the U.S. the entire food processing industry is moving toward more microbiologically clean production environments. This follows the lead of meat, poultry, egg, and dairy production where the risk is high and stringent cleaning methods like caustic washdowns and swabbing for contamination are the norm. These industries fall under the watchful eye of the USDA, a government agency with strict standards. (EHEDG plays this role in Europe.)
Our video provides insight into the key factors to consider in linear actuator selection for food production safety.