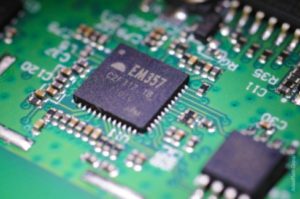
Electric rod actuators add accuracy and repeatability to PCB manufacturing
Some manufacturing processes require high precision -- printed circuit boards (PCB) production, for example. In these instances, the capabilities of each component in a production system are critical. Although machine designers know pneumatic cylinders well, these cylinders struggle to deliver the accuracy and repeatability demanded by high precision processes. Many design engineers now turn to electric rod actuators for accuracy and repeatability and for better operating efficiency.
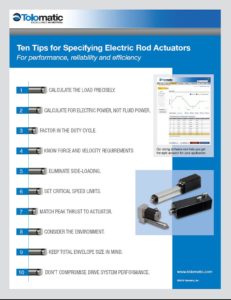
10 tips for specifying electric rod actuators: Part 2
In many applications electric rod actuators are a great solution. Compared to pneumatic or hydraulic cylinders, electric linear actuators offer more control over application parameters like position, velocity, and force. They deliver high degrees of accuracy and repeatability and can handle complex motion profiles. All things considered, an electric rod actuator is often the superior actuation choice.
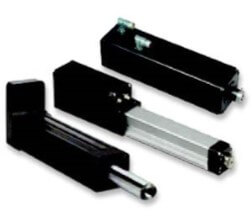
10 tips for specifying electric rod actuators: Part 1
There are lots of good reasons for specifying an electric rod actuator. Electric linear actuators offer a high degree of control over application parameters like position, velocity, and force. They deliver high degrees of accuracy and repeatability and can handle complex motion profiles. All things considered, an electric rod actuator is often a superior actuation choice compared to pneumatic or hydraulic cylinders.
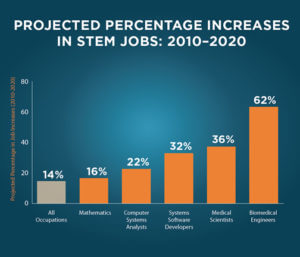
Supporting STEM education
Science, technology, engineering, and mathematics (together known as STEM) impart valuable life skills. STEM subjects teach students how to gather and evaluate evidence, make sense of information, and use new insights and knowledge to find solutions to complex problems.
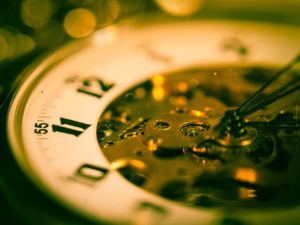
How to select electric linear actuators that stand the test of time
The length of time a linear actuator will function (i.e., service life) is critically important to a machine designer. Machines need to keep working reliably with little or no need for lengthy maintenance that will take a machine off-line . So, components like actuators must keep working.
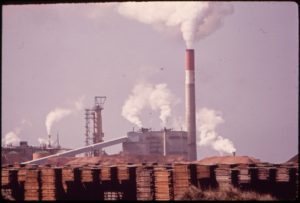
Electric high force linear actuator is tough enough to process lumber
The lumber industry has relied on the toughness and high force capabilities of hydraulic cylinders for years. But lately that reliance has been shaken. Hydraulic cylinders leak and can contaminate the fragile eco-systems in which lumber processing operates. Plus, hydraulic systems are only 40-55% efficient and cylinders require frequent maintenance. When combined, these factors can make hydraulic cylinders an expensive choice in the long run.
The introduction of electric high force linear actuators has given the lumber industry a new option for linear motion.
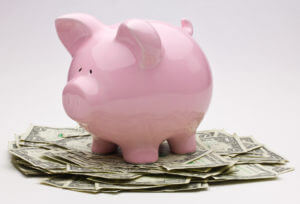
Total cost of ownership: pneumatic vs electric linear actuators
Who doesn’t like to save money? We’re all in search of a good deal, but how do you define what’s good? If you buy something on the cheap but it falls apart in a short time, is that a good deal? Maybe it’s smarter to pay more for something that last longer and performs better.
In business, this means considering total cost of ownership (TCO), that is, initial acquisition cost plus operating costs. Comparing TCO to purchase price alone is especially interesting when applied to pneumatic and electric linear actuators.
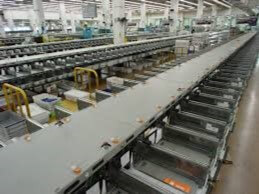
Electric cylinders essential to advanced conveyor system [Case Study]
Conveying systems are common in manufacturing. They can be straight-forward systems that take packages from point A to point B or complex ones for sorting and diverting. Systems used in food processing also must handle washdowns, a common practice in the industry.
As critical components, linear actuators must withstand the challenges of the application including environmental ones. Pneumatic cylinders have been used extensively in conveying. However, electric cylinder use is growing, fueled by demand for programmability and better accuracy.
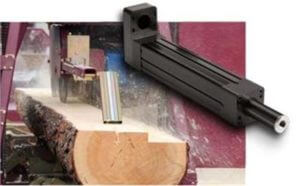
High force linear actuators – hydraulic vs electric [WEBINAR]
When your application calls for a high force linear actuator, you may believe that your only choice is a hydraulic cylinder. Hydraulics have long been the leading choice for automation equipment needing high force. However, now there are electric high force linear actuators that offer important advantages over hydraulics in terms of performance and total cost of ownership. Watch this webinar, and you may want to reconsider the merits of using an electric rod actuator.
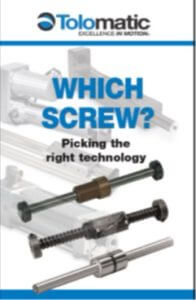
Which is best for high force linear actuators: Ball or roller screws?
If you’re selecting an electric high force linear actuator, you may believe you know the answer to the question in the headline. The force transmission prowess of roller screws is well known. But before you go to the expense of a roller screw linear actuator, take a careful look at the application. You may find that a ball screw actuator will do the job. And that could mean significant savings.