What’s best? Integrated linear actuators or traditional.
By Ryan Klemetson on January 15, 2020
When you’re faced with designing a new piece of automation equipment, you have a lot on your mind. Concerns like performance requirements. How to design flexibility into the machine so it can meet evolving demands. How to keep costs down – both purchase price and operating costs. How to pack the performance needed into a compact package.
If you need a linear motion system, you can turn to electric linear actuators because they address these issues. Electric actuators have inherent flexibility and long-term cost-efficiency.
Once you choose electric linear motion, you can select either an integrated linear actuator or a traditional design. Both options have pluses and minuses that we’ll review below in a high-level overview. For a full explanation of these decision factors, download our new white paper, Electric actuator technology comparison: Integrated and traditional designs.
Descriptions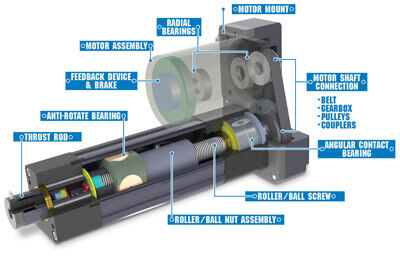
First, let’s define what we’re talking about when it comes to traditional and integrated linear actuators. A traditional actuator is an actuator with an external motor mounted to drive the screw assembly.
In this post we’ll use our RSA electric rod actuator (see image on right) as an example. The RSA Series includes both standard thrust and high thrust models.
Integrated linear actuators are defined by Tolomatic as a screw assembly rigidly coupled to and driven by an internal hollow-core servo motor.
The IMA linear servo actuator is shown here (on left). The IMA Series of linear servo actuators includes standard, stainless steel, and hygienic models.
Comparing integrated linear actuators and traditional
There are many factors a machine designer considers when deciding on an electric linear motion system. Let’s look at how these two technologies – traditional and integrated – perform on each of them.
- Ease of integration is a critical consideration when you’re building a machine.
Traditional actuators require that a motor be mounted to the actuator resulting in additional integration time. In this case, since the motor manufacturer often also makes the servo drive, integration of the motor, drive and controller is usually easy.
Integrated actuators eliminate motor-mounting time but may require time for entering motor parameters into the servo drive and then tuning the system.
- Size includes both envelope and weight considerations.
Traditional actuators can have their external motors mounted either inline or parallel to the actuator (also called reverse-parallel). Parallel mounting adds to the width of the configuration while inline motor mounting adds to the length.
Integrated actuators offer the most compact configuration.
The weight of a traditional actuator will vary depending on the motor.
In many applications, an integrated actuator may have an advantage due to reduced component count and envelope size. The reduced weight and size of an integrated actuator can further benefit some applications since the center of gravity is along the central axis.
- Ingress protection is particularly important in washdown and outdoor applications. Joints and fasteners create points where moisture and other contaminants can get into the actuator and cause corrosion.
Traditional actuators have many potential points of ingress due to the additional components necessary to adapt the actuator to the motor.
An integrated actuator has many fewer potential ingress points.There is no need to install a motor so this key ingress point is eliminated.
- Stroke length
Traditional actuators can have stroke lengths of up to 60 inches (1.5 meters).
Integrated actuators have limited stroke lengths, typically restricted to less than 18 inches (0.5 meters).
- Anti-rotation
The nut assembly support mechanism in a traditional actuator also serves the purpose of anti-rotation.
Integrated actuators require external anti-rotation, either in the machine design or with external provisions.
- Efficiency and reliability
Differences between actuators are driven by the number of torque transmission and rotating components in each system.
Traditional actuators have more components than integrated actuators.
- Positional accuracy and repeatability
Both traditional and integrated actuators can be specified with either ball or roller screws, so the relative accuracy and repeatability of these components are not issues. However, when it comes to backlash, it’s a different story.
The motor couplings in a traditional actuator can introduce backlash which negatively influences positional accuracy and repeatability.
Integrated actuators have a rigid connection between rotor and screw shaft so backlash is minimized when compared to traditional.
- Force capability
Traditional actuators can use large-diameter ball and roller screws, allowing force capabilities of up to 445 kN (100k lbf).
Integrated actuators limit the size of the screw to the size of the internal motor’s hollow core and available motor torque, giving them maximum force capabilities of about 54 kN (12k lbf).
- Ratings It is critical to factor in temperature rise limits of all components when using ratings provided by the actuator manufacturer.
Traditional actuators have more surface area for heat transfer, and the heat-generating components are separated from the motor to provide more efficient cooling. As a result, these actuators are better suited to applications where ambient temperatures are elevated.
The more compact design of an integrated actuator puts heat-generating components (motor, screw, bearings) close to each other. Due to this, the ability to cool the heat-generating components is decreased and can limit total actuator performance.
- Acceleration and responsiveness depend on servo motor factors as well as the stiffness of connections between the motor and screw assembly.
Traditional actuators use a variety of components (e.g., couplers, gearboxes, etc.) to pair a motor with the actuator. These connections can reduce mechanical stiffness between the motor and screw.
Integrated actuators have a rigid connection between rotor and screw assembly, creating a very stiff torque transmission system.
- Shock and vibration The distance between an actuator’s mounting face and the center of gravity affects the actuator’s sensitivity to shock and vibration.
In a traditional actuator a shock at the front-face mount is magnified about four times because the center of gravity is distant from the mounting surface.
In an integrated actuator the center of gravity is much closer to the mounting surface so shocks are magnified much less.
- Safety considerations (vertical loads) Safety may be an issue in vertical applications because power loss or component failure means the actuator will be unable to hold its load in position. Holding brakes are used on actuator motors in these applications.
With traditional actuators if the motor coupling, gearbox or belt fails, a brake will be unable to control the actuator load.
An integrated actuator has a rigid connection between the brake and the prime mover (screw). This eliminates the potential for falling loads in uncontrolled situations.
To summarize
There are many factors to consider when selecting a linear motion system.Each application will be unique. Some may call for a traditional electric linear actuator while others may be better served by an integrated linear actuator. If you have questions or need engineering input from linear motion experts, contact us.
Don’t forget this resource
For a full explanation of these decision factors, please download our new white paper, Electric actuator technology comparison: Integrated and traditional designs.