Stepper or servomotor? Selecting the best for your electric linear actuator.
By Tolomatic on January 13, 2015
When you specify an electric linear actuator for your application, you also need to specify a motor. The two basic types commonly used with linear actuators are stepper motors and servo motors. But what’s the difference? How do you choose? Here’s an explanation of the advantages and disadvantages of each motor type.
Stepper Motors
How They Work
A stepper motor is a brushless DC electric motor that divides a full rotation into a number of equal steps. In a stepper motor, the rotor has magnetic teeth that “lock in” or align to the electromagnetic poles in the stator.
The motor’s position is known by the number of input pulses or steps commanded. A common stepper motor moves 1.8° per step or has 200 steps per revolution. The motor's shaft can be commanded to move and hold at one of these steps without any feedback sensor.
Advantages
- A stepper motor is controlled accurately in open loop position control. No feedback information is needed to position the motor.
- The cost is usually lower than a servo motor’s because no position feedback sensor or associated cabling is required.
- These motors offer high torque at low speeds.
- They also have detent torque or torque at the output shaft when the motor is not energized and the shaft is rotated externally. When the system is powered down the detent torque can hold the actuator’s position. This can prevent the weight of the load from back driving the motor.
- Stepper motors deliver excellent repeatability. Accuracy is commonly within 3-5%.
Disadvantages
- Motor loses accuracy if there is insufficient torque to drive the load. In this case the motor may miss steps.
- To prevent lost steps, the motor is often sized 50% above the maximum torque required in the application. This may mean higher cost.
- Motor resonance is common and can result in torque loss and audible noise.
Servo Motors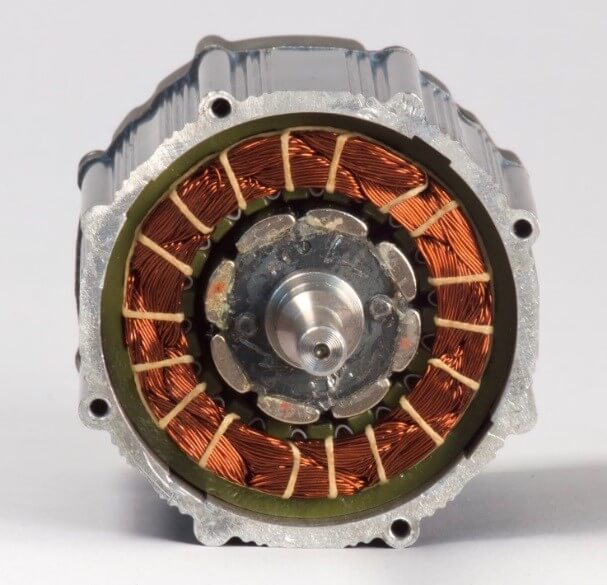
How They Work
A brushless servo motor has three wiring phases in the stator. The rotor has several pairs of permanent magnets aligned with alternating North and South poles. When the phase windings are energized, torque is generated between the phase’s electromagnet poles and the rotor’s magnetic poles causing the rotor to rotate. Speed is controlled by adjusting the amount of current in the phase winding. More current creates more torque to accelerate the rotor and load.
A servo motor is paired with some type of encoder to provide position and speed feedback. There are three ways to control a brushless servo:
- current/torque control
- velocity control
- position control
Often all three control types are available in a controller. They are usually regulated by a common PI or PID (Proportional Integral Differential) control scheme so the user can adjust the responsiveness of the system.
Advantages
- Servo systems offer a higher degree of control over variables such as position and speed.
- These systems offer a higher degree of accuracy than do stepper motors because they typically have feedback sensors and operate in closed loop control.
- Servo motors maintain torque throughout their speed range. They can also output brief periods of higher torque called “peak torque.”
Disadvantages
- Servo systems require more components and cabling. They are more complex and may cost more.
- Control loops for current, velocity, and position must be tuned to meet performance criteria. Tuning adds complexity to a servo system.
In Summary
Servo motors are generally used as high-performance alternatives to stepper motors, but higher performance comes at a cost. The encoder and controller of a servo system are an additional cost, but they optimize the performance of the overall system (speed, power, and accuracy).
The lack of feedback with a stepper motor limits its performance, and it can only drive a load that is well within its capacity.
Resources
Download our white paper for more information on this topic.