Servo welding actuators improve weld quality, reduce costs
By Gary Rosengren on November 3, 2015
Reducing manufacturing costs and improving product quality are driving forces in automotive manufacturing. Automation plays a key role in achieving these goals, and robots, especially welding robots, are an important part of the automation picture.
According to both an early-2015 Frost & Sullivan study and recent report by Research and Markets, the use of industrial welding robots is on the upswing globally, particularly in the automotive industry. This industry is investing in welding robots to boost efficiency and productivity. Plus, total cost of ownership of these industrial robots is going down so the technology is accessible to more manufacturers.
Resistance spot welding is used extensively in auto frame and body construction, and robotic welding lines are familiar sights in many plants. This type of welding requires speed, exact placement of welds, and precise pressure on weld tips. Most resistance spot welding robots rely on servo welding actuators to control cycle timing and pressure on weld tips. Because robots need to adjust to new car models, these linear actuators have to be easy to reprogram.
Electric servo actuators have many advantages over pneumatic cylinders But it’s crucial to specify the right electric actuator for the task. These brief case studies explain how the right servo welding actuator can improve manufacturing processes.
Auto body welding
An automotive plant performed spot welding using a servo actuator with external guide mechanism to operate a movable electrode. The guide mechanism was exposed to the hot welding environment, and expulsion from welds was contaminating it. This caused wear that increased the need for maintenance and shortened the assembly’s life. Maintenance and replacement caused downtime and loss of productivity.
A new servo welding actuator that had internal side loading support and anti-rotation functionality was installed. The actuator’s fully enclosed design provided protection from the harsh welding environment. The new servo actuator also delivered consistent force to the weld tips.
This change in actuators eliminates burn-throughs, reduces weld expulsion and ensures longer weld tip life. Reduced wear means less downtime for maintenance (e.g., greater productivity), and consistent weld tip force improves weld quality.
Auto chassis welding
An automotive plant was using a servo actuator with a reverse parallel style motor mount on their resistance spot welding robots. The combination had a large footprint and was very heavy. The manufacturer wanted a lighter weight, smaller actuator/robot combination.
A new servo welding actuator with an integrated servo motor reduces weight and saves space with its smaller footprint. The actuator eliminates the need for a timing belt transmission so there is less downtime for maintenance.
ServoWeld® Actuators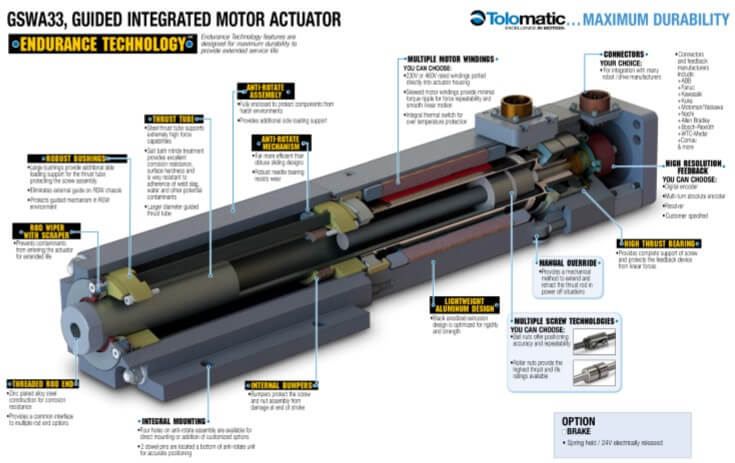
Tolomatic GSWA ServoWeld actuators offer accuracy, repeatability, infinite positioning flexibility, and programmability. They are lightweight and compact with an aluminum housing and integrated motor design. ServoWeld actuators, including our GSWA33, Guided models, are completely shielded to protect components from heat and contamination in the welding environment.
Download the ServoWeld catalog for an overview of the product line.
Learn more
Servo welding actuators like ServoWeld can help reduce costs and improve weld quality with shorter cycle times and exact weld tip pressure. Download our white paper to find out how.