Maximize Your Uptime With Electric Linear Actuators
By John Fenske on July 21, 2025
Engineers are increasingly enhancing industrial automation systems with electric actuators to eliminate downtime and increase throughput. These actuators are ideal for this growing demand because of their high reliability and performance while requiring very little maintenance. Historically, hydraulic and pneumatic actuators have been economically viable in many production environments, but frequent interruptions for maintenance can detract from their utility. To maximize the efficiency and output of an industrial manufacturing line, it’s crucial to minimize downtime as much as possible.
Electric actuators offer an alternative to pneumatic and hydraulic operations looking to eliminate downtime. Reliable, efficient and precise, they virtually eliminate downtime in demanding industrial automation applications because they feature fewer moving components and provide an easy pathway to predictive maintenance strategies. Often incorporating safety features to minimize the impact of mechanical failures, their high precision, accuracy and efficiency optimize many production processes and eliminate many repetitive manual procedures.
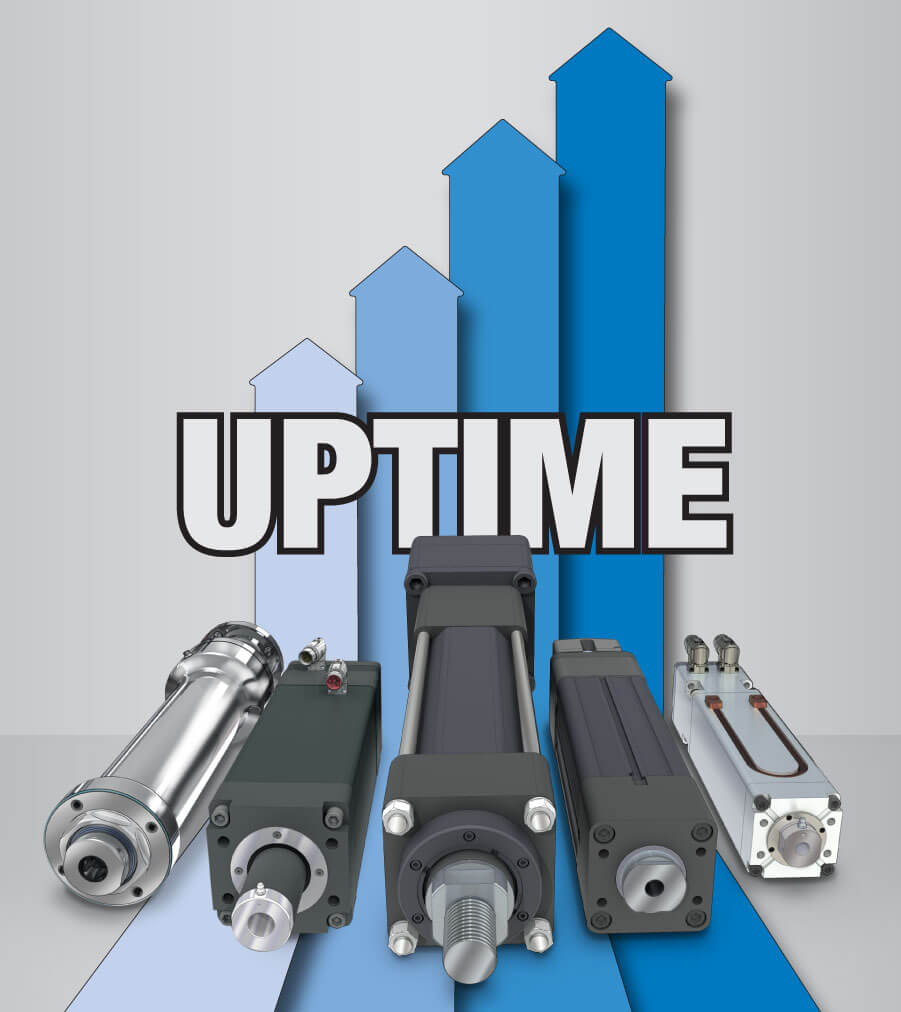
Fewer Parts
Pneumatic and hydraulic actuators may seem more economical at first, but the maintenance often required for such technologies can balloon costs beyond their initial investment. They require numerous components such as hoses, valves, filters, fittings and more — all of which are points of failure that require routine inspection, maintenance and replacement.
Featuring fewer components, electric actuators commonly only require a motor, an optional gearbox, cables and a drive or amplifier. Servo linear actuators go a step further by actually integrating the motor into the actuator design. Fewer moving parts means a lower risk of mechanical failures as well as reduced maintenance requirements.
Durable construction also prolongs electric actuator life. Most industrial electric actuators are built from high-quality materials to withstand rugged environments. Integrated servo linear actuator designs especially offer excellent protection. Containing the servomotor within the same housing as the actuator increases rigidity and ingress protection. This design minimizes the risk of mechanical failure that can interrupt an operation.
Longer Life
In addition to fewer parts, electric actuators also have a more predictable lifespan. Seals are necessary in hydraulic and pneumatic cylinders to maintain performance, and degradation is unavoidable. As they wear over time, cylinder performance drops due to pressure losses. It can be a challenge to predict when a seal will fail, but calculating electric actuator lifespan is much more predictable and consistent. Electric actuators also feature a seal around the rod, but performance is not directly affected.
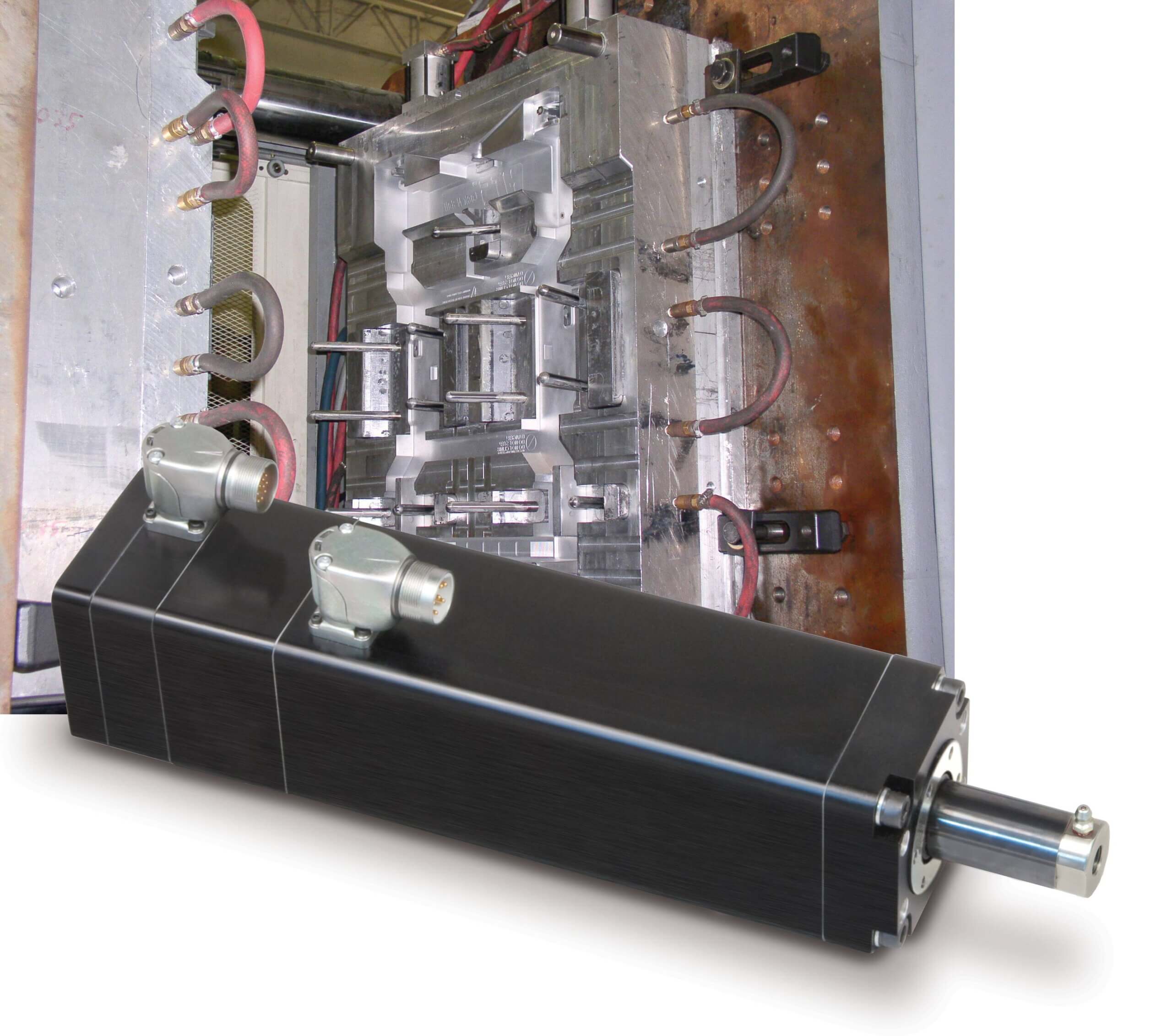
Predictive Maintenance
Tapping into electric actuator performance data can unlock predictive maintenance. While it is possible to implement sensors with pneumatic and hydraulic cylinders, such as flow meters on hoses, these strategies aren’t direct measurements that provide the most accurate picture of performance. On the other hand, electric actuators — especially servomotor-driven actuators — facilitate direct measurements of performance because they will often feature integrated sensors and provide motor feedback from the encoder.
This data enables real-time condition monitoring and enables predictive maintenance by applying machine learning algorithms to predict potential failures before they occur. By anticipating problems, unforeseen breakdowns are outright avoided and maintenance schedules can be optimized to minimize and prevent downtime.
Enhanced Safety
Even with predictive maintenance, accidents do happen. In the event of a failure, repercussions are felt throughout the entire manufacturing line that can grind production to a halt. Failures resulting in damage to the actuator or other equipment can extend unforeseen downtime for replacement and repairs.
Should downtime occur, actuators equipped with safety features can prevent damage. Even if downtime is unavoidable, it’s kept to a minimum by avoiding equipment replacement and repairs. Safety features like emergency stops or built-in overload protection help prevent mechanical damage. Fail-safe mechanisms like holding brakes will ensure that the actuators maintain safe operation during power loss or malfunction.
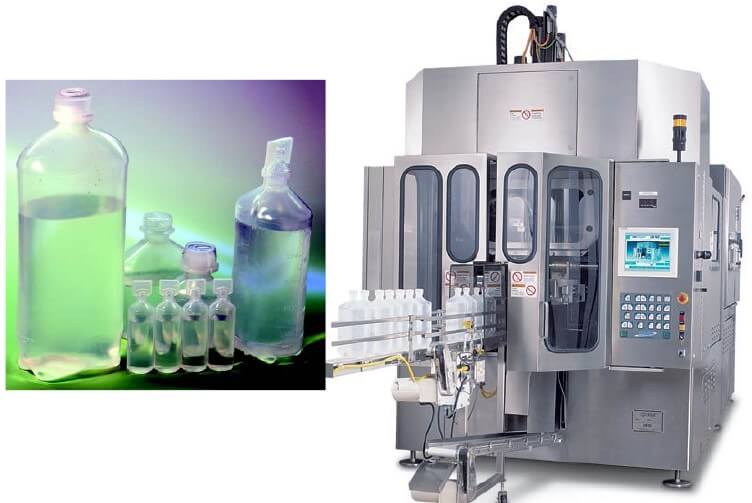
Precision, Accuracy and Efficiency
Electric actuators are more precise and accurate than their pneumatic and hydraulic counterparts. Traditional technologies require periodic adjustments to force, stroke length and more to maintain production consistency. However, electric actuators eliminate frequent calibrations and adjustments because of the precision and repeatability enabled by the control system. This level of control ensures the automation systems are optimized for long production runs.
Many industrial automation environments are maximizing uptime to meet demands for high output and efficiency. Implementing electric actuators into machine design is a valuable strategy to achieve this goal without compromises in cost or performance.
Interested in making the jump to electric? Learn more in our white paper.