Servomotorisches Punktschweißen bietet für die Autoproduktion herausragende Leistungswerte und senkt die Wartungskosten
Die weltweit führenden Automobilhersteller setzen auf robotergesteuerte servomotorische Schweißapparate zur Montage von Autokarosserien, damit im Vergleich mit herkömmlichen pneumatischen Punktsschweißmaschinen eine hohe Produktivität, niedrige Kosten und eine höhere Qualität sichergestellt werden.
Einführung
Die weltweit führenden Automobilhersteller setzen in erheblichem Maß auf Roboteranlagen. Nach Angaben der Internationalen Automobilherstellervereinigung stieg die Produktion in der Automobilindustrie weltweit um 30 % innerhalb des letzten Jahrzehnts an. Viele dieser Hersteller haben robotergetragene (oder statische) servogesteuerte Punktschweißmaschinen im Karosseriebau eingesetzt. Dafür gibt es gute Gründe, denn die Servosteuerung bietet für diesen Produktionsbereich viele Vorteile. Dazu gehören eine höhere Schweißqualität, eine höhere Produktivität, niedrigere Kosten sowie eine insgesamt höhere Produktqualität. Trotzdem produzieren viele Automobilhersteller immer noch Fahrzeuge für sonstige Märkte wie China, Brasilien, Korea, Indien und andere Länder vorwiegend mit herkömmlichen, manuell positionierbaren, pneumatisch angetriebenen Punktschweißmaschinen. Mit steigender Fahrzeugproduktion auf diesen Märkten und anspruchsvolleren Kundenbedürfnissen hinsichtlich der Qualität, überlegen diese Hersteller robotergetragene servogesteuerte Punktschweißmaschinen einzuführen, um auf dem weltweiten Markt konkurrenzfähig zu bleiben. In dieser Arbeit werden die Vorteile von elektrischen Servoantrieben gegenüber pneumatischen Antrieben für den Einsatz in robotergetragenen und stationären oder sockelmontierten Punktschweißmaschinen für die Automobilindustrie diskutiert.
Pneumatische Antriebe an Schweißzangen sind eine ausgereifte Technologie
In Fahrzeugproduktionsanlagen weltweit werden seit vielen Jahren pneumatisch angetriebene Punktschweißmaschinen sowohl mit manueller Positionierung als auch robotergetragene (und stationäre) Maschinen eingesetzt. Diese ausgereifte Technologie ist gut erforscht und verursacht
nur geringe Anschaffungskosten, dafür aber hohe Betriebskosten.
Im Allgemeinen hat die elektrische Servo-Punktschweißtechnologie einige Vorteile gegenüber der pneumatisch gesteuerten Punktschweißtechnologie. Hier ist vor allem die Festigkeit der Schweißstellen zu nennen. Dies liegt teilweise an unterschiedlichen Spannkraftleistungen der pneumatischen Zylinder von einer Schweißstelle zu nächsten. Steigender und fallender Versorgungsluftdruck, kleine Undichtheiten im System und Kontaminierung durch die Umwelt können eine Rolle bei steigender oder sinkender Kraftausbringung spielen. Wenn ein solcher Zustand erkannt wird, kann der Maschinenbediener den Druck auf die pneumatischen Zylinder erhöhen und so Festigkeitsprobleme abmindern, die auf eine zu geringe Schweißkraft zurückzuführen sind, wodurch jedoch andere Zustände verschlimmert werden können. Dazu gehört ein schnellerer Verschleiß der Schweißkappe, wodurch die Wartungsintensität ansteigt und in einigen Fällen sogar ein Durchbrennen die Folge sein kann. Darüber hinaus wird die Metallverdrängung durch das Schweißen am Schweißpunkt aufgrund hoher Kräfte verstärkt — insbesondere durch hohe Kontaktkräfte — weshalb vermehrt Schadstoffe in die Umwelt gelangen. Diese Zustände werden bei manuell positionierter Ausrüstung noch komplizierter, wodurch Schweißkappen ungenau ausgerichtet und/oder positioniert werden und es so zu einer schlechten Schweißqualität kommt, die eine redundante Positionierung oder zusätzliche Schweißpunkte erforderlich macht.
AUSWIRKUNGEN UNZUREICHENDER KLEMMKRAFT VON SCHWEISSPUNKT ZU SCHWEISSPUNKT
Abbildung 1: Undichte Stellen und Druckschwankungen können zu einer Reihe
unerfreulicher Ereignisse führen.
Bessere Kostenkontrolle mit Servosteuerungen
Die Betriebskosten für eine pneumatische Punktschweißmaschine kann in erheblichem Maße zu den Gesamtkosten des Herstellers für eine Karosserie beitragen. Hocheffiziente Druckluftkompressoren sind nicht nur sehr teuer in der Anschaffung, bei der Installation und Wartung, sondern auch notorische Stromfresser und erfordern oftmals Dauerbetrieb, damit eine ununterbrochene Versorgung mit Druckluft gewährleistet werden kann. Außerdem sind Undichtheiten bei hunderten Anschlüssen und Kilometern von Rohr- und Schlauchleitungen zur Versorgung mit Druckluft schon fast vorprogrammiert. Dadurch wird die Effizienz beeinträchtigt und die Betriebskosten steigen weiter.
Abbildung 2: Die obenstehende Tabelle zeigt die oftmals verborgenen Kosten von pneumatischem Schweißen.
Es gibt jedoch auch pneumatische Systeme, die „servo-pneumatische“ Geräte an Punktschweißmaschinen einsetzen. Diese Systeme lassen sich für eine Vielzahl verschiedener Funktionen programmieren, sind aber dennoch viel komplexer, da sie mit der Servosteuerung über ein komprimiertes Gemisch (Luft) fertig werden müssen. Auch wenn servo-pneumatische Systeme über zusätzliche Eigenschaften verfügen, wie beispielsweise Programmierbarkeit und zusätzliche Steuerung über konventionelle pneumatische Systeme, so sind sie immer noch hauptsächlich pneumatisch gesteuert und können ebenfalls Probleme wie Luftverlust und höhere Betriebskosten verursachen.
Elektrisch betriebene Servo-Punktschweißmaschinen haben zahlreiche Vorteile gegenüber pneumatischen und servo-pneumatischen Maschinen. Auch wenn die Anschaffungskosten eines Servoantriebs für den Einsatz auf einer Punkt-Schweißzange höher sind — in einigen Fällen bis zu fünfmal höher als pneumatisch betriebene — sind die Lebenszeitkosten niedriger. Bei einer Produktionsanlage mit 200 Schweißzangen würde die jährliche Stromkosteneinsparung (keine undichten Stellen vorausgesetzt) mehr als 90.000 USD betragen (siehe hierzu ROI-Kalkulation auf Seite 7). Daneben lassen sich Kosten durch einen weniger häufigen Schweißkappenaustausch einsparen, da die Bewegungen durch Servoantriebe vollständig gesteuert werden und die Schweißkappen durch geringere Einwirkungen langsamer verschleißen. Zusätzlich zu einem geringeren Schweißkappenverschleiß müssen die Spitzen seltener gefräst werden, wodurch sich der Kupferverlust an den Spitzen der Schweißkappen verringern lässt.
Wenn pro Schweißzange nur eine Schweißkappe weniger am Tag ersetzt werden muss, kann dies bis zu 100.000 USD an Kosten über einen Zeitraum von 5 Jahren einsparen. Die Tatsache, dass Servoantriebe länger halten, mehr Schweißungen als ein pneumatischer Zylinder absolvieren können und sehr flexibel einsetzbar sind, ermöglicht eine einfache Integration in neue Programme. Servoantriebe halten im Einsatz bei Widerstandspunktschweißungen bis zu 10 Mal länger als pneumatische Zylinder. Ebenfalls wird keine Druckluftversorgung für die zahlreichen Roboterachsen benötigt, wodurch keine Wartungsarbeiten für die Druckluftschläuche anfallen, die ansonsten aufgrund der Drehungen und komplexen Bewegungen des Roboters anfallen würden. Als Ergebnis lässt sich festhalten, dass sich durch den Einsatz eines servogesteuerten Systems die Lebenszeit und die Verlässlichkeit der Anlagen erhöhen lässt.
Servoantriebe ermöglichen Präzisionssteuerung
Beim Einsatz von Servosteuerungen ergeben sich noch weitaus mehr Vorteile. Der bedeutendste Vorteil besteht darin, dass die Bewegungen eines Servoantriebs sehr präzise gesteuert werden können. Denn das System kann so „programmiert“ werden, dass fast jeder Bewegungsablauf zu jeder Zeit bei einer hohen Wiederholungsrate und nahezu ohne redundante und unnötige Bewegungen ausgeführt werden kann.
Abbildung 3: Die obige Darstellung zeigt die kleinen präzisen Bewegungen an, die mit einem servo-gesteuerten Schweißprogramm möglich sind. Schnellere, hochqualitativer Schweißstellen sind möglich.
Ein typischer Schweißzyklus kann beispielsweise mit dem Öffnen oder dem Positionieren der Schweißzange dort beginnen, wo die Schweißkappen am weitesten entfernt sind. Als nächstes wird der Servomechanismus so „programmiert“, dass er eine schnelle oder eine Hochgeschwindigkeitsbewegung auf eine Position ausführt, die sich sehr nahe am zu schweißenden Material befindet. Dann berühren die Schweißspitzen das zu schweißende Material mit einer kontrollierten Geschwindigkeit, halten dieses mit einer konstanten Kraft während des Schweißvorgangs und nehmen wieder die Ausgangsposition neben dem Material ein, bevor sie auf die nächste Schweißposition bewegt werden. Diese Bewegung kann im Vergleich zu einem pneumatischen System viel gleichmäßiger durchgeführt werden, wodurch die Schweißkappen länger leben, eine konsistentere Schweißleistung abliefern und eine geringe Teiledeformation zur Folge haben. Eine Vielzahl von Schweißvorgängen findet bereits vor der Rückkehr der Schweißzange auf eine vollständig geöffnete Position statt, damit sofort am nächsten Bauteil weiter gemacht werden kann, wodurch sich Positionierungszeit einsparen lässt. Alle Bewegungen in einem servo-gesteuerten System sind hinsichtlich der Position, Kraft und Geschwindigkeit „programmierbar“, was für jedes zu schweißende Teil optimiert werden kann. Das, in Verbindung mit der Tatsache, dass alle Schweißvorgänge robotergesteuert sind, ermöglicht eine nahezu perfekte Synchronisierung aller Bewegungen und Schweißvorgänge. Daneben überwacht das System den Strom, der an den Servomotor abgegeben wird. Wenn die Schweißspitzen ihre Position eingenommen haben und die Quetschkraft erreicht wurde (basierend auf der Systemkalibrierung und den Drucktabellen), gibt das System ein Signal ab, dass es bereit zum Schweißen ist. Dadurch werden unnötige Wartezeiten oder Verzögerungen im Betriebsablauf vermieden. Zusätzlich ermöglicht eine vollständig interpolierte Bewegung von allen sieben Achsen, darunter auch der Servoantrieb an der Widerstandspunktschweißzange, eine optimale Bewegung der Schweißzange und einen Schweißvorgang mit maximalem Durchsatz und höchster Effizienz. Damit diese Vorteile erreicht werden können, ist es wichtig, eine zur siebenachsigen Robotersteuerung kompatible Feedback-Einrichtung einzusetzen.
Auf der anderen Seite verfügen pneumatische Systeme nur über eine eingeschränkte Möglichkeit, Positionen oder Geschwindigkeiten zu programmieren und die Kraft hängt vom Betriebsdruck ab. Tatsächlich neigen pneumatische System dazu, die Bauteile mit variabler Kraft abrupt zu berühren, bevor sie sich dann wieder abrupt auf die Ausgangsposition zurückbewegen und mit dem nächsten Schweißvorgang fortfahren. Aufgrund dessen bekamen pneumatische Systeme den Beinamen „Bang-Bang-Technologie“, weil sie sich abrupt auf die voreingestellten Positionen bewegen. Da sich pneumatische Systeme immer auf eine voreingestellte Position bewegen, ist die Strecke, die der pneumatische Zylinder zurücklegt, länger als die Strecke des Servoantriebs, weshalb zusätzliche Taktzeit erforderlich ist. Außerdem wird das Signal „Schweißen“ bei pneumatisch betriebenen Schweißzangen erst dann gesendet, wenn die sechs Achsen des Roboters die Schweißzange in Position gebracht haben. An dieser Stelle wird das Schweißsignal über einen „zeitbasierten“ Befehl statt über einen „wenn-bereit-basierten“ Befehl gesendet, der erst nach Berührung der Schweißspitzen (gesteuert über die pneumatischen Zylinder) mit dem Bauteil erfolgt. Der zeitbasierte Befehl ist wichtig, den die Bewegungszeit der Schweißspitze (oder des Luftzylinders) variiert auf Grundlage der Druckverluste bei der Druckluftversorgung, sowie aufgrund der gemeinsamen Druckluftnutzung von nebeneinanderliegenden Schweißzangen und pneumatischen Zylindern.
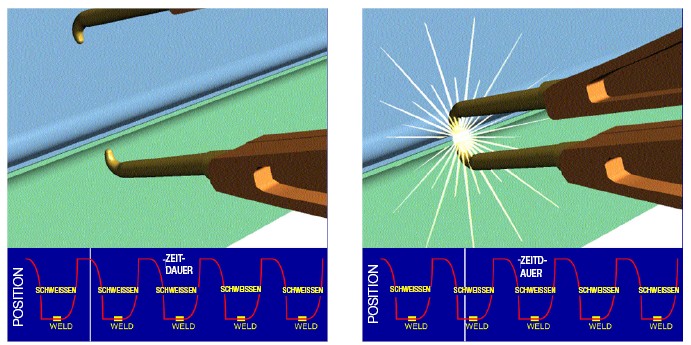
Abbildung 4: Pneumatische Punktschweißungen erfordern eine größere Öffnung, wodurch sich der Schweißvorgang im Vergleich zur Servo-Punktschweißtechnik verlangsamt und vermehrt Schadstoff in die Umgebung abgegeben werden.
Abbildung 5: Das obenstehende Diagramm zeigt eine Reduzierung der Schweißzyklen unter Verwendung eines servogesteuerten „bereit-zum-Schweißen“-Signals gegenüber einem pneumatischen „zeitbasierten“ Befehl.
Wie diese Diagramme und Schaubilder zeigen, kann die Servo-Schweißtechnologie die Taktzeit verringern und den Durchsatz erhöhen. Daneben werden oftmals weniger Schweißzangenstationen bei der Fahrzeugproduktion benötigt, da die Schweißtaktzeiteffizienz optimiert wurde, und so weitere Kosten- und Wartungseinsparungen zu erwarten sind.
Programmierbarkeit erhöht die Qualität
Die Möglichkeit ein Servosystem auf wichtige Betriebsmerkmale
„programmieren“ zu können, erhöht automatisch die Ausbringungsqualität. Die kontrollierte Geschwindigkeit und Kraft, mit der die Bauteile konfrontiert werden, erhöhen die Spannkraftleistung während des Schweißvorgangs.
Als Ergebnis dessen sinkt die Metallverdrängung, der Verschleiß der
Schweißkappen reduziert sich, die Schweißkappen müssen seltener
abgefräst werden, ein Durchbrennen wird verhindert und die Zahl
redundanter Schweißungen, die für eine ordnungsgemäße Bauteilintegrität erforderlich wären, sinkt ebenfalls. Wenn man die robotergetragene
Servo-Punktschweißmaschine mit manuell positionierenden pneumatischen Punktschweißgeräten vergleicht, wiegen die Vorteile sogar noch größer. Mit der Eliminierung menschlicher Fehlerquellen bei der Positionierung der Punktschweißgeräte, wird die Schweißqualität sowie die Bauteilqualität stark verbessert. Roboter haben die Fähigkeit, das Punktschweißgerät sehr genau zu positionieren. Deshalb können Schweißungen genau dort vorgenommen werden, wo sie benötigt werden. Und Roboter können Schweißungen dort vornehmen, wo sich ein Mensch in Gefahr begeben würde.
Die Tatsache, dass sich servogesteuerte Punktschweißmaschinen „programmieren“ lassen, hat noch weitere Vorteile. Ein Servosystem kann beispielsweise neu programmiert werden. Das bedeutet, dass das System für andere Aufgaben umstrukturiert oder wiederverwendet werden kann. Dadurch kann der Fahrzeugbauer nicht nur die Vorteile aus der Programmierbarkeit nutzen, sondern er kann die Ausrüstung auch bei der Produktion anderer Fahrzeugarten einsetzen, wodurch er den maximalen Vorteil aus dem Roboter und der servo-gesteuerten Schweißmaschine ziehen kann. Oftmals lässt sich dadurch der erforderliche ROI auf Sachkapital erreichen. Dies kann insbesondere in Schwellenländern von Vorteil sein, wo das Fahrzeugproduktionsvolumen geringer ausfällt und eine vollständig robotisierte Anlage für nur einen Fahrzeugtyp nicht rechtfertigt.
Die Investitionsrentabilität kann weniger als eineinhalb Jahre dauern
Zusammenfassend lässt sich festhalten, dass servogesteuerte Schweißzangen bei der Widerstandpunktschweißung im Automobilbereich eine höhere Schweißqualität bieten, Wartungsarbeiten minimieren, Wartungskosten senken, das Geräteleben verlängern und einen besseren ROI vorweisen als pneumatische Schweißzangen. Bei all diesen Vorteilen haben einige Hersteller den ROI für eine robotergetragene servogesteuerte Schweißzange in hochvolumigen Produktionseinrichtungen auf weniger als eineinhalb Jahre errechnet.* Fahrzeughersteller, die derzeit von Hand positionierte oder robotergesteuerte pneumatische Punktschweißmaschinen einsetzen, sollten die Vorteile von robotergesteuerten Servo-Schweißgeräten analysieren. Sehr oft führt dies zu einer Verbesserung der Herstellungsqualität und die einhergehenden Wettbewerbsvorteile rechtfertigen eine solche Investition allenfalls.
* Siehe ROI-Tabellen von pneumatischen Antrieben im Vergleich zu elektrischen Antrieben bei pneumatisch-gesteuerten/servo-gesteuerten Schweißzangen auf Seite 8.
ROI BEI PNEUMATISCHEN ANTRIEBEN IM VERGLEICH ZU ELEKTRISCHEN ANTRIEBEN BEI PNEUMATISCH-/SERVO-GESTEUERTEN SCHWEISSZANGEN
Im folgenden Modell wird eine Produktionsstätte mit 200 Schweißzangen angenommen, wobei hier nicht die Einsparungen aus erhöhter Produktion durch elektrische Schweißzangen oder Einsparungen beim Kaufpreis für Schweißzangen eingerechnet wurden.
*Die oben geschätzten Kosten für die Pneumatik basieren auf einem Antrieb plus die erforderlichen Luftkomponenten; die oben geschätzten Kosten für die Elektrik basieren auf einem elektrischen Antrieb, einem Motor, Kabel und einer Steuerung.
DATENANNAHMEN
• Geschätzte Lebenszeit eines elektrischen Antriebs (Anzahl von Schweißungen): 20.000.000
• Geschätzte Lebenszeit eines pneumatischen Antriebs (Anzahl von Schweißungen): 3.000.000
• Instandsetzungen eines pneumatischen Antriebs (Anzahl von Schweißungen): 1.000.000
• Instandsetzungen eines elektrischen Antriebs (Anzahl von Schweißungen): 10.000.000
• Wartung der Pneumatik (Material und Arbeit): 250,00 $
• Wartung der Elektrik (Material und Arbeit): 750,00 $
• Großvolumige Produktion (Schweißungen/Jahr): 5.000.000 ~ 1000 Fahrzeugen * 15 Schweißvorgänge an jedem Fahrzeug pro Schweißzange * 350 Produktionstage
• Niedrigvolumige Produktion (Schweißungen/Jahr): 1.500.000 ~ 300 Fahrzeugen * 15 Schweißvorgänge an jedem Fahrzeug pro Schweißzange * 350 Produktionstage
• Effizienz des pneumatischen Systems: 17,5 %
• Effizienz des elektrischen Systems: 74 %
• Stromkosten (kW/h): 0,07 $
• Luftleck von 6,35 mm (1/4″)/jährliche Kosten: 11.735,00 $ bei Annahme von Luftleck für eine Infrastruktur von
200 Einheiten im Werk für P-/S-gesteuerte Maschinen beträgt ca. 6,35 mm (1/4″)
Tolomatic ist ein führender Lieferant für elektrisch und pneumatisch gesteuerte lineare Antriebe. Zu den Kernkompetenzen von Tolomatic gehören lineare Antriebe, servogesteuerte Antriebe mit hoher Schubleistung, Servo- und Schrittmotoren, Steuerungen und konfigurierte lineare Systeme. Standardprodukte werden auf Bestellung hergestellt und sind in höchstens fünf Tagen lieferbereit. Daneben stellt Tolomatic auch Winkelgetriebe, Sattelbremsen und Kupplungen her.
Im Allgemeinen hat die elektrische Servo-Punktschweiß-technologie einige Vorteile gegenüber der pneumatisch gesteuerten Punktschweißtechnologie. Hier ist vor allem die Festigkeit der Schweißstellen zu nennen.
Servoantriebe sind im Einsatz bei Widerstandspunktschweißungen bis zu 10 Mal länger haltbar als pneumatische Zylinder.
Bewegungen eines Servoantriebs können sehr präzise gesteuert werden.
Alle Bewegungen in einem servo-gesteuerten System sind hinsichtlich der Position, Kraft und Geschwindigkeit „programmierbar“, was für jedes zu schweißende Teil optimiert werden kann.
Auf der anderen Seite verfügen pneumatische Systeme nur über eine eingeschränkte Möglichkeit, Positionen oder Geschwindigkeiten zu programmieren und die Kraft hängt vom Betriebsdruck ab.
Die Möglichkeit ein Servosystem auf wichtige Betriebsmerkmale „programmieren“ zu können, erhöht automatisch die Ausbringungsqualität.
Ein servogesteuertes System kann für andere Aufgaben umstrukturiert oder wiederverwendet werden. Dadurch kann der Fahrzeugbauer nicht nur die Vorteile aus der Programmierbarkeit nutzen, sondern er kann die Ausrüstung auch bei der Produktion anderer Fahrzeugarten einsetzen, wodurch er den maximalen Vorteil aus dem Roboter und der servo-gesteuerten Schweißmaschine ziehen kann.
Tolomatic bietet eine Reihe von ServoWeld® Punktschweißantrieben, die einige herausragende Vorteile gegenüber pneumatisch betriebenen Anlagen bieten. Die Unterschiede werden in der Tabelle rechts dargestellt.
Für weitere Informationen bezüglich des ServoWeld® Antriebs besuchen Sie bitte unsere Webseite unter www.tolomatic.com und downloaden
Sie unsere Broschüre.